ATOS 5
Chase the microns
ATOS 5 provides high-quality 3D data for inspecting airfoil profiles in drive and power station turbines
Each individual component of gas turbines and jet engines must function reliably under extreme conditions. Huge physical forces constantly impact the airfoils and the surrounding structural parts in operation. Engineers must be able to identify minute changes in materials and technology across the entire life cycle – from construction and production through to regular maintenance. Even small deviations can lead to malfunctions with far-reaching consequences. This is where GOM systems come into play, as they are capable of making a significant contribution in test processes.
A multipurpose test system for parts with high requirements
Thanks to ATOS 5, a high-resolution optical digitizer, GOM’s portfolio now includes a specialist device that is perfectly suited to carry out 2D and 3D airfoil inspections. Highly complex geometrics – such as freeform surfaces and narrow edges of fan blades, blisks, or monocrystalline casting parts – can be examined and measured precisely as part of a component inspection process. Quality engineers benefit from the detailed 3D models, which help to understand and quantify existing deviations in manufacturing processes. These models display color deviation representations of actual and nominal data, such as 2D and 3D analyses of shape, position, and thickness.
An ideal data basis for simulations
When gases or gas mixtures meet the blades of a turbine, this produces air flows that can only be simulated with a great deal of calculation. The forces that have an impact on these parts must be identified as effectively as possible so they can operate safely and efficiently. GOM systems can generate a digital twin of the actual component, meaning this data is then available for additional simulations as a further advancement in the standard inspection and analysis of individual components.
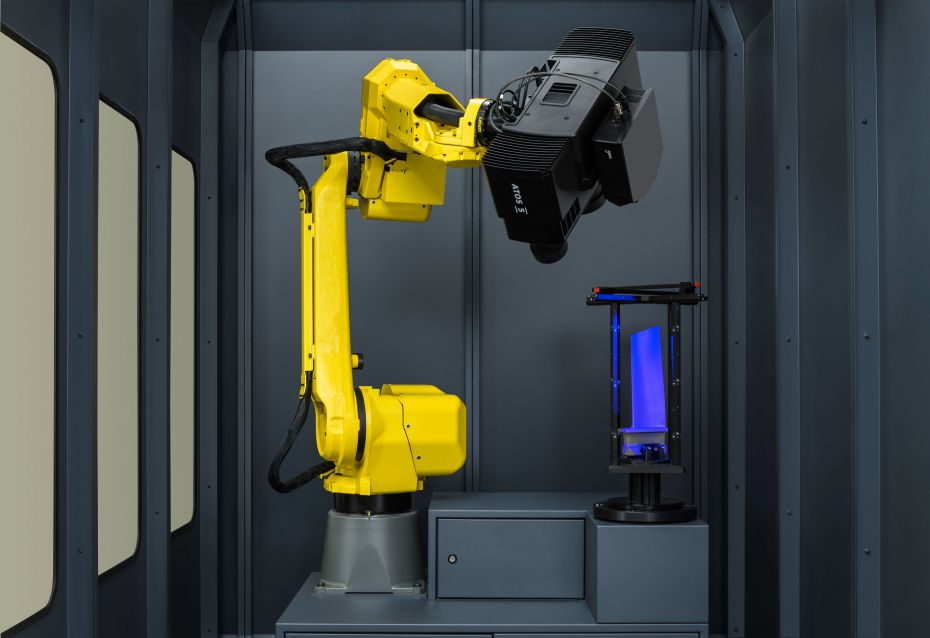
Custom inspection of airfoils
- ATOS ScanBox including virtual measuring room (VMR)
- Automated photogrammetry
- Kiosk Interface for fully automatic inspection
- GOM Inspect and GOM Inspect Professional
- Inspection of specific sections
- Radial inspections between profile sections possible
- Construction tools for company-specific inspection principles
Learn more about ATOS 5
https://www.gom.com/metrology-systems/atos/atos-5.html