Batteries in electric vehicles
Let’s Join Forces and Bring the Future onto the Road
The market for electric vehicles is rapidly growing on a global scale.
In 2021, it was a first that a battery electric vehicle was the best-selling passenger car in Europe – the Tesla Model 3. The increasing demand for New Energy Vehicles (NEVs) means that manufacturers and their suppliers have to speed up their engineering efforts and their production – which poses new challenges for quality assurance processes. Batteries are components that are especially relevant for the e-vehicle’s safety and structure.
Accordingly, customers are expecting higher capacities, i.e. a higher range per single charge. If you want to build reliable batteries with a long service life, you won’t be able to bypass the highest quality standards: Cells, modules and battery trays must be manufactured to strict tolerances. This is why a wide range of imaging, analysis and metrology solutions is crucial for battery research as well as for quality control of batteries and battery trays.
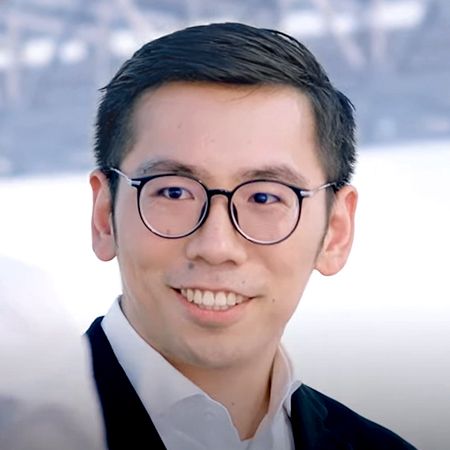
“Batteries are at the core of electric vehicles. Their quality assurance has top priority for manufacturers. It is simply a MUST.”
Quality assurance for batteries is a complex process: Different measuring techniques are used to inspect battery characteristics, such as material, electrode, cell, module and battery tray.
Industrial microscopy is used to analyze microstructures and potential impurities during battery development. The ZEISS Crossbeam scanning electron microscope (SEM), for example, can use an ion beam to expose relevant areas of interest below the surface and analyze them in the nanometer range.
During production, on the other hand, nondestructive analyses are used for battery cells and modules. In this phase, mostly X-ray and computed tomography systems (CT) are employed.
The battery tray – also known as a battery carrier – is another important component in New Energy Vehicles. It is no longer just a component but has been fully integrated into the car body and is thus also crucial for its stability. Battery trays have to pass several quality gates during production so as to meet safety requirements and to ensure the quality of the vehicle.
One of these gates visualizes the geometry evaluation in its entirety. Flatness, fitting accuracy and sealing areas of the battery carrier – all of these aspects have an impact on the dimensional accuracy of the entire body. The battery modules have to be inserted correctly into the battery chambers with thermal compound in order to ensure safe operation.
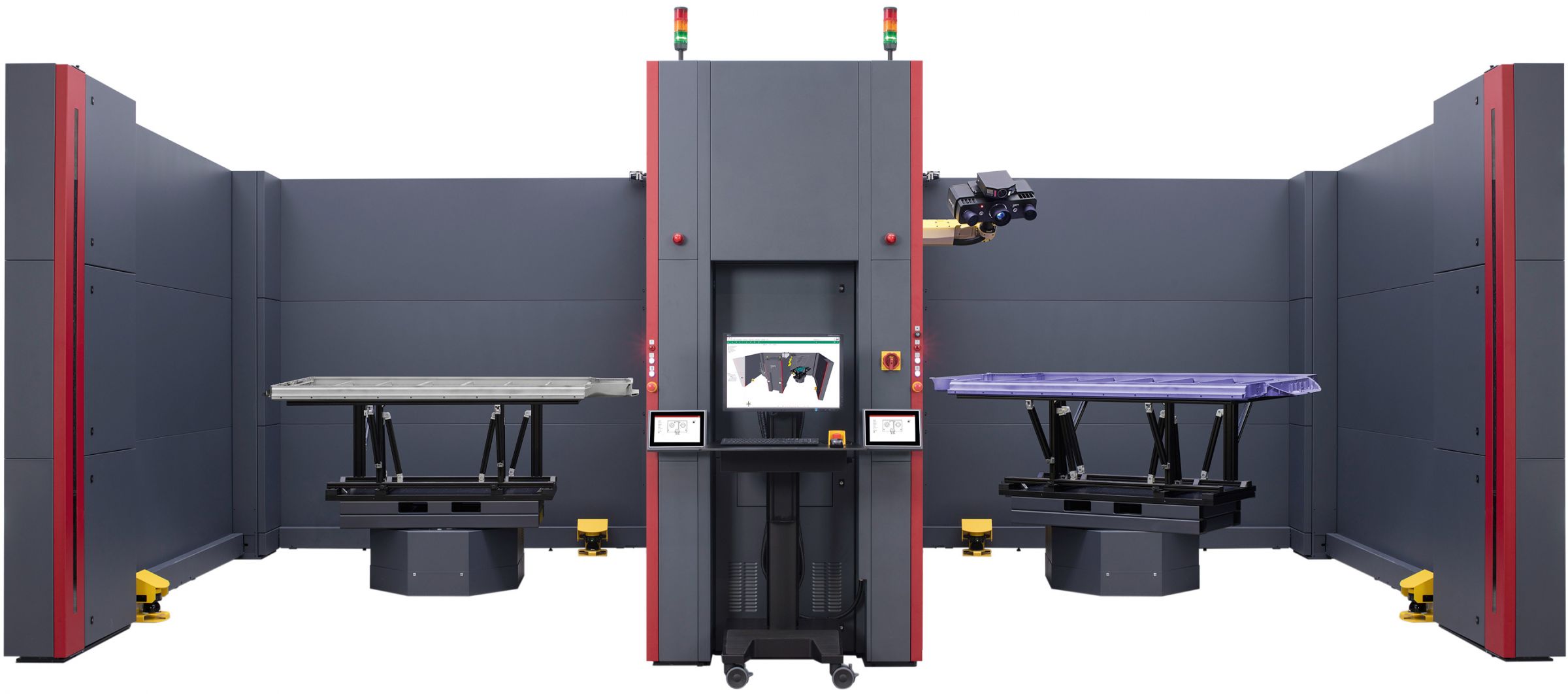
ATOS ScanBox is available for various applications, up to the complete measurement of entire car bodies.
The optical 3D measuring machine ATOS ScanBox comes with the preinstalled GOM Inspect Pro software and automatically scans the component. It then creates a digital geometric twin both from the battery tray and the battery pack itself. The entire inspection of relevant characteristics, such as the flatness of the battery chambers and the position of connecting holes, takes just a few minutes. Users can evaluate inspection characteristics that are relevant for the process as statistical trends, e.g. to identify gap width changes caused by thermal deformations of the battery module. Finally, a simulation shows the virtual assembly of the tray, the modules and the wiring in the body in order to forecast the quality of the assembly process. The analysis covers all the important steps in battery tray production: from aluminum extrusion to casting and welding over adhesive application down to milling, drilling and riveting processes.
A special efficiency booster: The optical 3D measuring machine’s software uses the component’s CAD data for fully automated teach-in programming of robot positions and paths. The measurement technology is traceable and meets ISO 10360 requirements. ATOS ScanBox captures entire geometries at low noise levels, even on dark or shiny surfaces.
ZEISS eMobility Solutions
Measurements, inspections and data delivery – the broad technology portfolio of ZEISS offers professional solutions for every process step in quality assurance. Light, electron and X-ray microscopy, computed tomography systems (CT), and coordinate and optical 3D measuring machines carry out inspections of your component’s structure, composition and dimensional accuracy in order to improve and ensure the safety, reliability and capacity of e-vehicles.
Computed tomography systems in battery production
In order to meet the demand for NEVs with a higher range, the battery cells’ energy density has to be boosted without increasing their weight and size. This ever-growing density necessitates more sophisticated X-rays during nondestructive inspections. Also, the details to be inspected have become significantly smaller: Today, some of the features barely measure 10 micrometers.
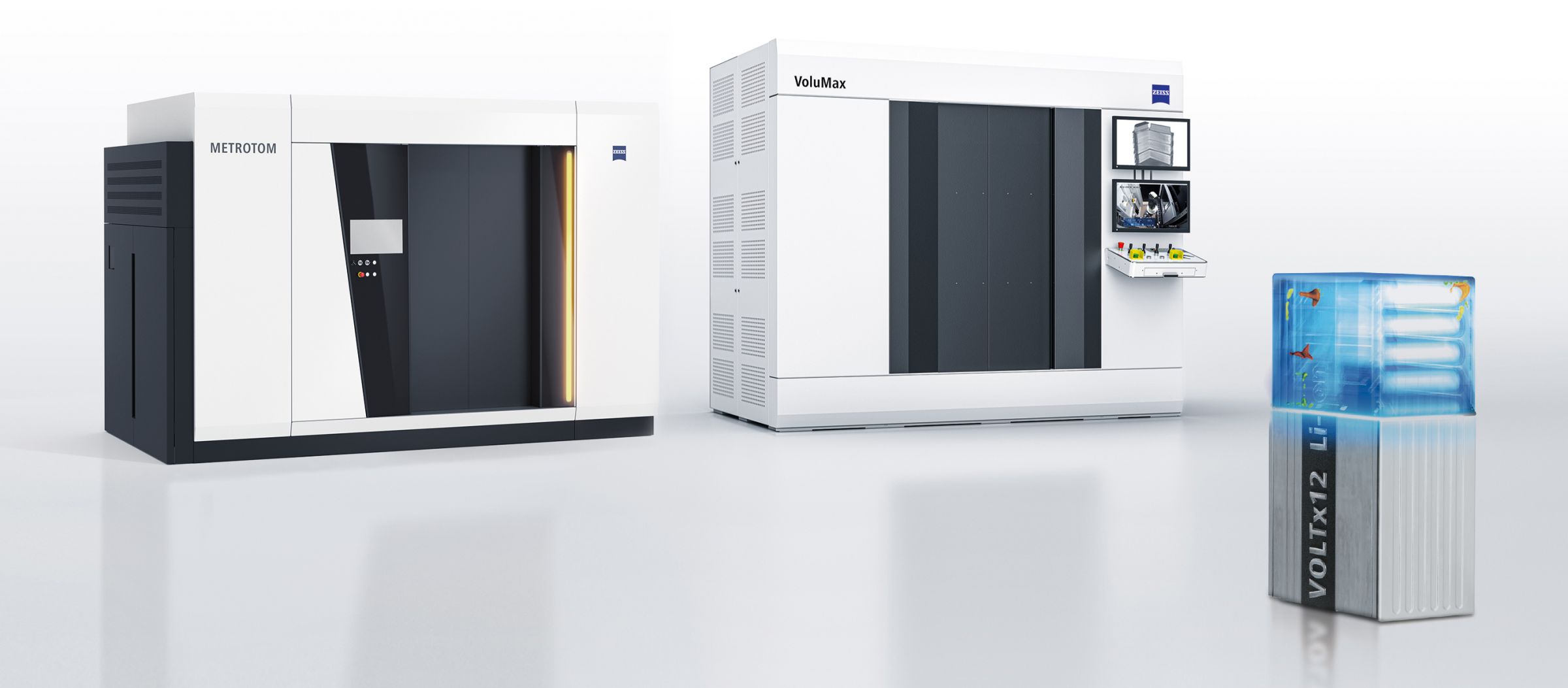
CT systems such as ZEISS VoluMax 9 titan and ZEISS METROTOM 1500 perform consistent X-ray scans of dense parts such as battery modules. They generate very high-resolution 3D volume data sets, thus rendering hidden defects and characteristics, e.g. electrode defects, misalignments, overhangs, housing pores and particle contaminations. The latter are a major safety risk and must not be part of the final product. CT systems efficiently solve complex measurement and inspection tasks with just one X-ray scan. This is indispensable for both battery capacity and safety.
Scanning electron microscopes in battery development: ZEISS Crossbeam combines the imaging and analysis power of a high-resolution field emission scanning electron microscope (FE-SEM) with the processing features of a focused ion beam (FIB).
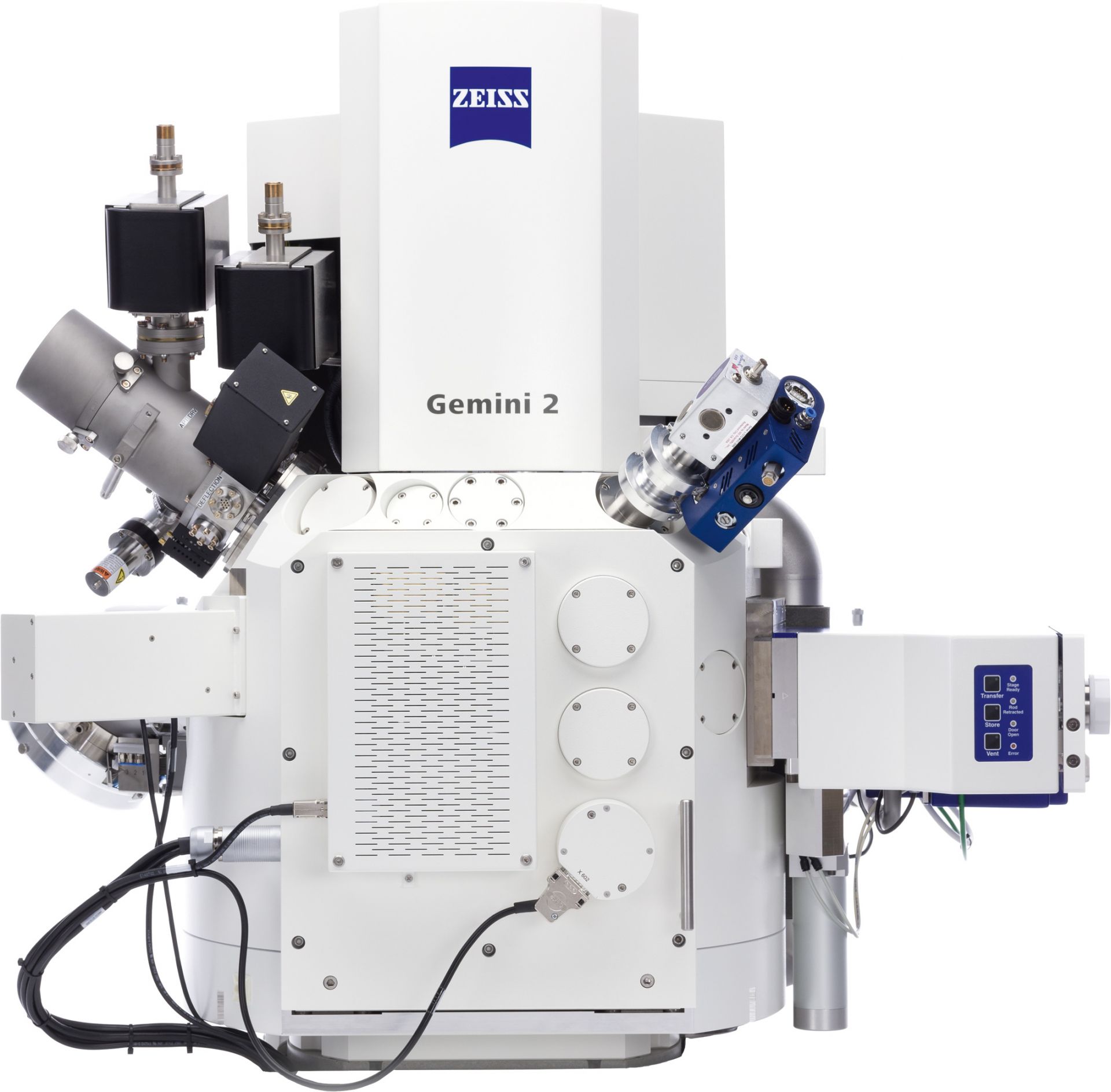